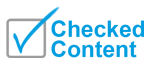
Airbus A380
About this schools Wikipedia selection
Arranging a Wikipedia selection for schools in the developing world without internet was an initiative by SOS Children. Visit the SOS Children website at http://www.soschildren.org/
Airbus A380 | |
---|---|
The A380 during its World Tour flight 2006-2007. | |
Role | Airliner |
Manufacturer | Airbus |
First flight | 27 April 2005 |
Primary user | Singapore Airlines |
Produced | 2002 – present |
Number built | 11 as of December 2007 |
Program cost | €12 ($17.1) billion |
Unit cost | $319.2 million |
The Airbus A380 is a double-deck, four-engine airliner manufactured by the European corporation Airbus, an EADS subsidiary. The largest passenger airliner in the world, the A380 made its maiden flight on 27 April 2005 from Toulouse, France, and made its first commercial flight on 25 October 2007 from Singapore to Sydney with Singapore Airlines. The aircraft was known as the Airbus A3XX during much of its development phase, but the nickname Superjumbo has since become associated with it.
The A380's upper deck extends along the entire length of the fuselage. This allows for a cabin with 50% more floor space than the next largest airliner, the Boeing 747-400, and provides seating for 525 people in standard three-class configuration or up to 853 people in full economy class configuration. The A380 is offered in passenger and freighter versions. The A380-800, the passenger model, is the largest passenger airliner in the world, superseding the Boeing 747, but has a shorter fuselage than the Airbus A340-600 which is Airbus' next biggest passenger aeroplane. The A380-800F, the freighter model, is offered as one of the largest freight aircraft, with a listed payload capacity exceeded only by the Antonov An-225. The A380-800 has a design range of 15,200 kilometres (8,200 nmi), sufficient to fly from New York to Hong Kong for example, and a cruising speed of Mach 0.85 (about 900 km/h or 560 mph at cruise altitude).
History
Development
Airbus started the development of a very large airliner (termed Megaliner by Airbus in the early development stages) in the early 1990s, both to complete its own range of products and to break the dominance that Boeing had enjoyed in this market segment since the early 1970s with its 747. McDonnell Douglas pursued a similar strategy with its ultimately unsuccessful MD-12 design. As each manufacturer looked to build a successor to the 747, they knew there was room for only one new aircraft to be profitable in the 600 to 800 seat market segment. Each knew the risk of splitting such a niche market, as had been demonstrated by the simultaneous debut of the Lockheed L-1011 and the McDonnell Douglas DC-10: both planes met the market’s needs, but the market could profitably sustain only one model, eventually resulting in Lockheed's departure from the civil airliner business. In January 1993, Boeing and several companies in the Airbus consortium started a joint feasibility study of an aircraft known as the Very Large Commercial Transport (VLCT), aiming to form a partnership to share the limited market.
In June 1994, Airbus began developing its own very large airliner, designated the A3XX. Airbus considered several designs, including an odd side-by-side combination of two fuselages from the A340, which was Airbus’s largest jet at the time. The A3XX was pitted against the VLCT study and Boeing’s own New Large Aircraft successor to the 747, which evolved into the 747X, a stretched version of the 747 with the fore body "hump" extended rearwards to accommodate more passengers. The joint VLCT effort ended in July 1996, and Boeing suspended the 747X program in January 1997. From 1997 to 2000, as the East Asian financial crisis darkened the market outlook, Airbus refined its design, targeting a 15 to 20 percent reduction in operating costs over the existing Boeing 747-400. The A3XX design converged on a double-decker layout that provided more passenger volume than a traditional single-deck design.

On 19 December 2000, the supervisory board of newly restructured Airbus voted to launch a €8.8 billion program to build the A3XX, re-christened as the A380, with 55 orders from six launch customers. The A380 designation was a break from previous Airbus families, which had progressed sequentially from A300 to A340. It was chosen because the number 8 resembles the double-deck cross section, and is a lucky number in some Asian countries where the aircraft was being marketed. The aircraft’s final configuration was frozen in early 2001, and manufacturing of the first A380 wing box component started on 23 January 2002. The development cost of the A380 had grown to €11 billion when the first aircraft was completed.
Boeing, meanwhile, resurrected the 747X programme several times before finally launching the 747-8 Intercontinental in November 2005 (with entry into service planned for 2009). Boeing chose to develop a derivative for the 400 to 500 seat market, instead of matching the A380's capacity.
Testing
Five A380s were built for testing and demonstration purposes. The first prototype, serial number MSN001 and registration F-WWOW, was unveiled at a ceremony in Toulouse on 18 January 2005. Its maiden flight took place at 8:29 UTC (10:29 a.m. local time) 27 April 2005. The prototype, equipped with Trent 900 engines, departed runway 32L of Toulouse Blagnac International Airport with a flight crew of six headed by chief test pilot Jacques Rosay, carrying 20 tonnes (22 short tons) of flight test instrumentation and water ballast. The take-off weight of the aircraft was 421 tonnes (464 short tons); although this was only 75 percent of its maximum take-off weight, it was the heaviest take-off weight of any passenger airliner ever flown.
In mid-November 2005, the A380 embarked on a tour of Southeast Asia and Australia for promotional and for long-haul flight testing purposes, visiting Singapore, Brisbane, Sydney, Melbourne and Kuala Lumpur. During this tour, the livery of Singapore Airlines, Qantas and Malaysia Airlines were applied in addition to the Airbus house livery. On 19 November, an A380 flew in full Emirates livery at the Dubai Air Show.
On 1 December 2005, the A380 achieved its maximum design speed of Mach 0.96, in a shallow dive, completing the opening of the flight envelope. The aircraft's maximum allowed operational speed is lower, at Mach 0.89, and its cruising speed is Mach 0.85.
On 10 January 2006, the A380 made its first transatlantic flight to Medellín in Colombia, to test engine performance at a high altitude airport. It arrived in North America on 6 February, landing in Iqaluit, Nunavut in Canada for cold-weather testing. The same aircraft then flew to Singapore to participate in the Asian Aerospace 2006 exhibition, in full Singapore Airlines livery.
On 26 March 2006, the A380 underwent evacuation certification in Hamburg in Germany. With 8 of the 16 exits blocked, 853 passengers and 20 crew left the aircraft in 78 seconds, less than the 90 seconds required by certification standards. Three days later, the A380 received European Aviation Safety Agency (EASA) and United States Federal Aviation Administration (FAA) approval to carry up to 853 passengers.
The first A380 planned for delivery to a customer, serial number MSN003 and registration F-WWSA, took to the air in May 2006. The maiden flight of the first A380 with GP7200 engines serial number MSN009 and registration F-WWEA took place on 25 August 2006.
On 4 September 2006, the first full passenger-carrying flight test took place. The aircraft flew from Toulouse with 474 Airbus employees on board, in the first of a series of flights to test passenger facilities and comfort. In November 2006, a further series of route proving flights took place to demonstrate the aircraft's performance for 150 flight hours under typical airline operating conditions.
Airbus obtained type certificate for the A380-841 and A380-842 model from the EASA and FAA on 12 December 2006 in a joint ceremony at the company's French headquarters. The A380-861 model obtained the type certificate 14 December 2007.
As of December 2007, eleven A380s have flown, and the five A380s in the test programme had logged over 4,565 hours during 1,364 flights, including route proving and demonstration flights. As of December 11th 2007, the A380 has visited 26 countries: Argentina, Australia, Brazil, Canada, China, Colombia, Ethiopia, France, Germany, Iceland, India, Ireland, Japan, Malaysia, Norway, Philippines, Portugal, Singapore, South Africa, South Korea, Spain, Thailand, Turkey, the United Arab Emirates, the United Kingdom, United States of America and Vietnam.
Delivery delays
Initial production of the A380 was plagued by delays attributed to the 530 km (330 miles) of wiring in each aircraft. Airbus cited as underlying causes the complexity of the cabin wiring (100,000 wires and 40,300 connectors), its concurrent design and production, the high degree of customisation for each airline, and failures of configuration management and change control. Deliveries would be pushed back by nearly two years.
Specifically, it would appear that German and Spanish Airbus facilities continued to use CATIA version 4, while British and French sites migrated to version 5. This caused overall configuration management problems, at least in part because wiring harnesses manufactured using aluminium rather than copper conductors necessitated special design rules including non-standard dimensions and bend radii: these were not easily transferred between different versions of the software.
While Airbus attributes the delays entirely to wiring, industry analyst Richard Aboulafia, noting that the first A380 will be around 5.5 tons heavier than intended, speculates that the weight problems "[go] a long way in explaining the delay", and that "wiring alone did not explain what we were all hearing. It sounds like weight-reduction design changes are a big part of the delay, too."
Airbus announced the first delay in June 2005 and notified airlines that delivery would slip by six months, with Singapore Airlines expecting the first A380 in the last quarter of 2006, Qantas getting its first delivery in April 2007 and Emirates receiving aircraft before 2008. This reduced the number of planned deliveries by the end of 2009 from about 120 to 90–100.
On 13 June 2006, Airbus announced a second delay, with the delivery schedule undergoing an additional shift of six to seven months. Although the first delivery was still planned before the end of 2006, deliveries in 2007 would drop to only 9 aircraft, and deliveries by the end of 2009 would be cut to 70–80 aircraft. The announcement caused a 26% drop in the share price of Airbus's parent, EADS, and led to the departure of EADS CEO Noël Forgeard, Airbus CEO Gustav Humbert, and A380 programme manager Charles Champion. In the wake of the new delay, Malaysia Airlines and ILFC were reported to be considering the cancellation of their orders. Launch customers Singapore Airlines, Emirates and Qantas also were reported to be angered by the delays and expecting compensation. However, on 21 July 2006, Singapore Airlines ordered a further 9 A380s and stated that Airbus had "demonstrated to our satisfaction that the engineering design for the A380 is sound [and that] it has performed well in flight and certification tests and the delays in its delivery have been caused more by production, rather than technical, issues."
On 3 October 2006, upon completion of a review of the A380 program, the then CEO of Airbus, Christian Streiff, announced a third delay, pushing the first delivery for Singapore Airlines to October 2007, to be followed by 13 deliveries in 2008, 25 in 2009, and the full production rate of 45 aircraft per year in 2010. The delay also increased the earnings shortfall projected by Airbus through 2010 to €4.8 billion. The customer with the largest A380 order, Emirates, saw its first delivery pushed back to August 2008 and said as a result that it was considering scaling back its order, potentially in favour of the rival Boeing 747-8. However, Emirates never scaled back the order but placed additional orders for A380s in 2007. Virgin Atlantic deferred its deliveries by four years, to 2013. The third delay was followed by the first cancellations to hit the A380 programme. On 7 November 2006 FedEx cancelled its order for 10 A380F freighters in favour of 15 Boeing 777 Freighters. In March 2007, the last remaining customer for the A380F, UPS, announced the cancellation of its order. Airbus suspended work on the freighter version in order to concentrate on delivering the passenger version, but said the freighter remained on offer. As of March 2007, Airbus estimated a 2014 entry into service for the A380F.
Entry into service
The first aircraft sold, MSN003, was handed over on 15 October 2007, following a lengthy acceptance test phase, and entered into service on 25 October 2007 with a commercial flight between Singapore and Sydney (flight number SQ380). The plane was given the registration number 9V-SKA. Two months later Singapore Airlines CEO Chew Choong Seng said that the A380 was performing better than both the airline and Airbus had anticipated, burning 20% less fuel per passenger than the airline's existing 747-400 fleet. Singapore Airlines plans to use its first three aircraft, in a 471-seat configuration, on its London–Singapore–Sydney service; until then the A380 will be used between Sydney and Singapore. Subsequent routes may include the Singapore–San Francisco route via Hong Kong, as well as direct flights to Paris, Narita and Frankfurt. The second A380 for Singapore Airlines, MSN005, was handed over by Airbus on 11 January 2008 and registered as 9V-SKB.
The first aircraft for Qantas (second airline to take delivery of the A380), MSN014, was approaching final wiring installation in September 2007 and was expected to be shipped to Hamburg for cabin fitting out by the end of 2007. Qantas has announced it will use the A380, in a 450-seat configuration, on its Melbourne and Sydney to Los Angeles and Melbourne and Sydney to London routes.
The first Engine Alliance powered A380 MSN011, which is due to enter service with Emirates Airline, had its maiden flight on 4 September 2007. Emirates will receive the aircraft in September 2008 and will initially deploy the plane on its Australian services to Sydney and shortly after to Melbourne. Air France has said that its A380s will be used on its Paris to Montreal and New York routes.
As of October 2007 Airbus had assembled 23 A380s, and was expecting the first aircraft equipped with the new electrical system (which replaces the root cause of the massive programme delays), MSN026, to be ready for 'power-on' in early 2008.
Design
The new Airbus is sold in two models. The A380-800 was originally designed to carry 555 passengers in a three-class configuration or 853 passengers (538 on the main deck and 315 on the upper deck) in a single-class economy configuration. In May 2007, Airbus began marketing the same aircraft to customers with 30 fewer passengers (now 525 passengers) traded for 200 nmi more range, to better reflect trends in premium class accommodation. The design range for the -800 model is 15,200 km (8,200 nmi). The second model, the A380-800F freighter, will carry 150 tonnes of cargo 10,400 km (5,600 nmi). Future variants may include an A380-900 stretch seating about 656 passengers (or up to 960 passengers in an all economy configuration) and an extended range version with the same passenger capacity as the A380-800.
The A380's wing is sized for a Maximum Take-Off Weight (MTOW) over 650 tonnes in order to accommodate these future versions, albeit with some strengthening required. The stronger wing (and structure) is used on the A380-800F freighter. This common design approach sacrifices some fuel efficiency on the A380-800 passenger model, but Airbus estimates that the size of the aircraft, coupled with the advances in technology described below, will provide lower operating costs per passenger than all current variants of Boeing 747. The A380 also features wingtip fences similar to those found on the A310 and A320 to alleviate the effects of wake turbulence, increasing fuel efficiency and performance.
Flight deck
Airbus used similar cockpit layout, procedures and handling characteristics to those of other Airbus aircraft, to reduce crew training costs. Accordingly, the A380 features an improved glass cockpit, and fly-by-wire flight controls linked to side-sticks. The improved cockpit displays feature eight 15-by-20 cm (6-by-8-inch) liquid crystal displays, all of which are physically identical and interchangeable. These comprise two Primary Flight Displays, two navigation displays, one engine parameter display, one system display and two Multi-Function Displays. These MFDs are new with the A380, and provide an easy-to-use interface to the flight management system—replacing three multifunction control and display units. They include QWERTY keyboards and trackballs, interfacing with a graphical " point-and-click" display navigation system.
Engines
The A380 can be fitted with two different types of engines: A380-841, A380-842 and A380-843F with Rolls-Royce Trent 900, and the A380-861 and A380-863F with Engine Alliance GP7000 turbofans. The Trent 900 is a derivative of the Trent 800, and the GP7000 has roots from the GE90 and PW4000. The Trent 900 core is a scaled version of the Trent 500, but incorporates the swept fan technology of the stillborn Trent 8104. The GP7200 has a GE90-derived core and PW4090-derived fan and low-pressure turbo-machinery. Only two of the four engines are fitted with reverse thrusters.
Noise reduction was an important requirement in the A380's design, and particularly affects engine design. Both engine types allow the aircraft to achieve QC/2 departure and QC/0.5 arrival noise limits under the Quota Count system set by London Heathrow Airport, which is expected to become a key destination for the A380.
Advanced materials
Whilst most of the fuselage is aluminium, composite materials make up 25% of the A380's airframe, by weight. Carbon-fibre reinforced plastic, glass-fibre reinforced plastic and quartz-fibre reinforced plastic are used extensively in wings, fuselage sections (such as the undercarriage and rear end of fuselage), tail surfaces, and doors. The A380 is the first commercial airliner with a central wing box made of carbon fibre reinforced plastic, and it is the first to have a wing cross-section that is smoothly contoured. Other commercial airliners have wings that are partitioned span-wise in sections. The flowing, continuous cross-section allows for maximum aerodynamic efficiency. Thermoplastics are used in the leading edges of the slats. The new material GLARE (GLAss-REinforced fibre metal laminate) is used in the upper fuselage and on the stabilizers' leading edges. This aluminium- glass-fibre laminate is lighter and has better corrosion and impact resistance than conventional aluminium alloys used in aviation. Unlike earlier composite materials, it can be repaired using conventional aluminium repair techniques. Newer weldable aluminium alloys are also used. This enables the widespread use of laser beam welding manufacturing techniques — eliminating rows of rivets and resulting in a lighter, stronger structure.
Avionics architecture
The A380 employs an Integrated Modular Avionics (IMA) architecture, first used in advanced military aircraft such as the F-22 Raptor and the Eurofighter Typhoon. It is based on a commercial off-the-shelf (COTS) design. Many previous dedicated single-purpose avionics computers are replaced by dedicated software housed in onboard processor modules and servers. This cuts the number of parts, provides increased flexibility without resorting to customised avionics, and reduces costs by using commercially available computing power. Together with IMA, the A380 avionics are very highly networked. The data communication networks use Avionics Full-Duplex Switched Ethernet, following the ARINC 664 standard. The data networks are switched, full-duplexed, star-topology and based on 100baseTX fast-Ethernet. This reduces the amount of wiring required and minimizes latency. The Network Systems Server (NSS) is the heart of A380 paperless cockpit. It eliminates the bulky manuals and charts traditionally carried by the pilots. The NSS has enough inbuilt robustness to do away with onboard backup paper documents. The A380's network and server system stores data and offers electronic documentation, providing a required equipment list, navigation charts, performance calculations, and an aircraft logbook. All are accessible to the pilot from two additional 27 cm (11 inch) diagonal LCDs, each controlled by its own keyboard and control cursor device mounted in the foldable table in front of each pilot.
Systems
Power-by-wire flight control actuators are used for the first time in civil service, backing up the primary hydraulic flight control actuators. During certain maneuvers, they augment the primary actuators. They have self-contained hydraulic and electrical power supplies. They are used as electro-hydrostatic actuators (EHA) in the aileron and elevator, and as electrical backup hydrostatic actuators (EBHA) for the rudder and some spoilers.
The aircraft's 350 bar (35 MPa or 5,000 psi) hydraulic system is an improvement over the typical 210 bar (21 MPa or 3,000 psi) system found in other commercial aircraft since the 1940s. First used in military aircraft, higher pressure hydraulics reduce the size of pipelines, actuators and other components for overall weight reduction. The 350 bar pressure is generated by eight de-clutchable hydraulic pumps. Pipelines are typically made from titanium and the system features both fuel and air-cooled heat exchangers. The hydraulics system architecture also differs significantly from other airliners. Self-contained electrically powered hydraulic power packs, instead of a secondary hydraulic system, are the backups for the primary systems. This saves weight and reduces maintenance.
The A380 uses four 150 kVA variable-frequency electrical generators eliminating the constant speed drives for better reliability. The A380 uses aluminium power cables instead of copper for greater weight savings due to the number of cables used for an aircraft of this size and complexity. The electrical power system is fully computerized and many contactors and breakers have been replaced by solid-state devices for better performance and increased reliability.
The A380 features a bulbless illumination system. LEDs are employed in the cabin, cockpit, cargo and other fuselage areas. The cabin lighting features programmable multi-spectral LEDs capable of creating a cabin ambience simulating daylight, night or shades in between. On the outside of the aircraft, HID lighting is used to give brighter, whiter and better quality illumination. These two technologies provide brightness and a service life superior to traditional incandescent light bulbs.
The A380 was initially planned without thrust reversers, as Airbus believed it to have ample braking capacity. The FAA disagreed, and Airbus elected to fit only the two inboard engines with them. The two outboard engines do not have reversers, reducing the amount of debris stirred up during landing. The A380 features electrically actuated thrust reversers, giving them better reliability than their pneumatic or hydraulic equivalents, in addition to saving weight.
Passenger provisions
The A380 produces 50% less cabin noise than a 747 and has higher cabin air pressure (equivalent to an altitude of 1500 metres (5000 feet) versus 2500 metres (8000 feet)); both features are expected to reduce the effects of travel fatigue. The upper and lower decks are connected by two stairways, fore and aft, wide enough to accommodate two passengers side-by-side. In a 555-passenger configuration, the A380 has 33% more seats than a 747-400 in a standard three-class configuration but 50% more cabin area and volume, resulting in more space per passenger. Its maximum certified carrying capacity is 853 passengers in an all-economy-class configuration.
Compared to a 747, the A380 has larger windows and overhead bins, and 60 cm (2 feet) of extra headroom. The wider cabin allows for 48 cm (19 inch) wide economy seats instead of 43 cm (17 inch) seats on a 747, although the seat pitch of 81 cm (32 inch) is the same as that on a 747. Singapore Airline's economy-class seats feature 27 cm (10.6 inch) LCD screens in each seatback, as well as an AC power supply in most seats; business-class seats are 84 cm (34 inches) wide, can lay flat for sleeping, and have 39 cm (15.4 inch) LCD screens.
Airbus' initial publicity stressed the comfort and space of the A380's cabin, anticipating installations such as relaxation areas, bars, duty-free shops, and beauty salons. Virgin Atlantic Airways already offers a bar as part of its "Upper Class" service on its A340 and 747 aircraft, and has announced plans to include casinos, double beds, and gymnasiums on its A380s. Singapore Airlines offers twelve fully-enclosed first-class suites on its A380, each with one full and one secondary seat, full-sized bed, desk, personal storage, and 58-cm (23-inch) LCD screen at a 20% to 25% price premium over standard first class seating. Four of these suites are in the form of two "double" suites featuring a double bed. Emirates has not yet revealed their front-end A380 product although Qantas Airways has shown their product which features a long flat-bed that converts from the seat but does not have privacy doors.
Production
Major structural sections of the A380 are built in France, Germany, Spain, and the United Kingdom. Due to their size, they are brought to the assembly hall in Toulouse in France by surface transportation, rather than by the A300-600ST Beluga aircraft used for other Airbus models. Components of the A380 are provided by suppliers from around the world; the five largest contributors, by value, are Rolls-Royce, SAFRAN, United Technologies, General Electric, and Goodrich.
The front and rear sections of the fuselage are loaded on an Airbus Roll-on/roll-off (RORO) ship, Ville de Bordeaux, in Hamburg in northern Germany, whence they are shipped to the United Kingdom. The wings, which are manufactured at Filton in Bristol and Broughton in North Wales, are transported by barge to Mostyn docks, where the ship adds them to its cargo. In Saint-Nazaire in western France, the ship trades the fuselage sections from Hamburg for larger, assembled sections, some of which include the nose. The ship unloads in Bordeaux. Afterwards, the ship picks up the belly and tail sections by Construcciones Aeronáuticas SA in Cádiz in southern Spain, and delivers them to Bordeaux. From there, the A380 parts are transported by barge to Langon, and by oversize road convoys to the assembly hall in Toulouse. New wider roads, canal systems and barges were developed to deliver the A380 parts. After assembly, the aircraft are flown to Hamburg, XFW to be furnished and painted. It takes 3,600 litres (950 gallons) of paint to cover the 3,100 m² (33,000 ft²) exterior of an A380.
Airbus sized the production facilities and supply chain for a production rate of four A380s per month.
Orders and deliveries
![]() |
Eighteen customers have ordered the A380, including an order from aircraft lessor ILFC. Total orders for the A380 stand at 193, of which 189 were firm as of 31 December 2007. Orders for the freighter model reached 27 but dwindled to zero following the production delays. Airbus expects to sell a total of 750 aircraft, and estimated break-even at 420 units, increased from 270 due to the delays and the falling exchange rate of the US dollar. In April 2007, Airbus CEO Louis Gallois said that break-even had risen further, but declined to give the new figure. Industry analysts anticipate between 400 and 880 sales by 2025. As of 2006, the list price of an A380 was US$ 296 to 316 million, depending on equipment installed.
The first private buyer of an A380 for personal use is Saudi Prince Alwaleed bin Talal, who reportedly spent only fifteen minutes on the plane before deciding to put one under contract.
Industry sources have stated that the United States Air Force Air Mobility Command is looking into possibly purchasing the A380 as a replacement for the aging Boeing 747s in the role of presidential transport. The USAF may also be interested in a military version of the A380F as a tactical transport aircraft, replacing the C-5 Galaxy.
Deliveries
2007 | 2008 | 2009 | 2010 | Total |
1 | 1 (13) | (25) | (44) | 2 (83) |
Anticipated yearly totals are in parentheses.
Technical concerns
Several concerns about the A380 have arisen during its development. Airbus has addressed these concerns as required to obtain a type certificate from the European Aviation Safety Agency and its American counterpart, the Federal Aviation Administration.
Ground operations
Early critics claimed that the A380 would damage taxiways and other airport surfaces. However, the pressure exerted by its wheels is lower than that of a Boeing 747 or Boeing 777 because the A380 has 22 wheels, four more than the 747, and eight more than the 777. Airbus measured pavement loads using a 540-tonne (595 short tons) ballasted test rig, designed to replicate the landing gear of the A380. The rig was towed over a section of pavement at Airbus' facilities that had been instrumented with embedded load sensors.
Based on its wingspan, the U.S. FAA classifies the A380 as a Design Group VI aircraft, and originally required a width of 60 m (200 ft) for runways and 30 m (100 ft) for taxiways, compared with 45 m (150 ft) and 23 m (75 ft) for Design Group V aircraft such as the Boeing 747. The FAA also considered limiting the taxi speed of the A380 to 25 km/h (15 mph) when operating on Group V infrastructure, but issued waivers related to the speed restriction and some of the proposed runway widening requirements. Airbus claimed from the beginning that the A380 could safely operate on Group V runways and taxiways, without the need for widening. In July 2007, the FAA and EASA agreed to let the A380 operate on 45 m runways without restrictions. The International Civil Aviation Organization (ICAO) is still disputing this issue.
The A380 was designed to fit within an 80 × 80 m airport gate, and can land or take off on any runway that can accommodate a Boeing 747. Its large wingspan can require some taxiway and apron reconfigurations, to maintain safe separation margins when two of the aircraft pass each other. Taxiway shoulders may be required to be paved to reduce the likelihood of foreign object damage caused to (or by) the outboard engines, which overhang more than 25 m (80 ft) from the centre line of the aircraft. Any taxiway or runway bridge must be capable of supporting the A380's maximum weight. The terminal gate must be sized such that the A380's wings do not block adjacent gates, and may also provide multiple jetway bridges for simultaneous boarding on both decks.
Service vehicles with lifts capable of reaching the upper deck should be obtained, as well as tractors capable of handling the A380's maximum ramp weight. The A380 test aircraft have participated in a campaign of airport compatibility testing to verify the modifications already made at several large airports, visiting a number of airports around the world.
Wake turbulence
The A380 generates more wake turbulence on takeoff and landing than existing aircraft types, requiring increased airport approach and departure spacing for following aircraft.
In 2005, the ICAO recommended that provisional separation criteria for the A380 be substantially greater than for the 747 because preliminary flight test data suggested a stronger wake than the 747. These criteria were in effect while the A380 Wake Vortex Steering Group, with representatives from the JAA, Eurocontrol, the FAA, and Airbus, refined its 3-year study of the issue with additional flight testing. In September 2006, the working group presented its conclusions to the ICAO, which rendered final guidance on the issue in November 2006. The working group concluded that an aircraft trailing an A380 during approach needs to maintain a separation of 6 nmi, 8 nmi and 10 nmi respectively for ICAO "Heavy", "Medium", and "Light" aircraft categories, compared with 4 nmi, 5 nmi and 6 nmi spacing for other heavy aircraft. However, the working group found no need to limit the A380's trailing distance behind another aircraft, potentially making up for some of the increased spacing behind the A380. On departure behind an A380, the working group concluded that "Heavy" aircraft are required to wait two minutes, and "Medium"/"Light" aircraft three minutes for time based operations. Finally, the working group did not recommend any modified restrictions on vertical or horizontal separation criteria during cruise.
During the A380's maiden trip to the United States in 2007, air traffic control used the callsign suffix "Super" to distinguish the A380 from " Heavy" aircraft.
Wing strength
During the destructive wing strength certification test on MSN5000, the test wing of the A380 failed to meet the certification requirement of 150% of limit load. Limit load is the maximum load expected during operation in the design life of an aircraft. The test wing buckled between the inboard and outboard engines at 147% of limit load, as the wing tip reached a vertical deflection of 7.4 m (24.3 ft). Airbus initially stated that the test article represented an early design, and that the load requirement would be verified by analysis of changes already made. Subsequently, Airbus announced that modifications adding 30 kg to the wing would be made to provide the required strength.
Future versions
Airbus A380-900
Airbus top sales executive and COO John Leahy confirmed the plans for an enlarged version, the A380-900. This version would have a seat capacity of 650 passengers in standard configuration, and of around 900 passengers in economy-only configuration. The development of the A380-900 is planned to start once the regular production of the A380-800 variant reaches 40 planes per year. Airbus foresees to reach this production capacity in 2010. Given this timeline, the first A380-900s could be delivered to customers around 2015, hence at about the same time as the freighter variant A380-800F. Airlines, including Emirates , Virgin Atlantic , and Cathay Pacific , along with leasing company ILFC have already expressed great interest in the extended model. According to an interview in Airliner World magazine's December issue, Singapore Airlines CEO Chew Choon Seng revealed at the delivery of their first A380-800 that the airline is keeping their options open with their order, by only defining their first ten A380s as -800s. The remaining 9 aircraft could be in fact be transferred to -900s.
Specifications


Measurement | A380-800 | A380-800F |
---|---|---|
Cockpit crew | Two | |
Seating capacity | 525 (3-class) 644 (2-class) 853 (1-class) |
12 couriers |
Length | 73 m (239 ft 6 in) | |
Span | 79.8 m (261 ft 10 in) | |
Height | 24.1 m (79 ft 1 in) | |
Wheelbase | 30.4 m (99 ft 8 in) | |
Outside fuselage width | 7.14 m (23 ft 6 in) | |
Cabin width, main deck | 6.60 m (21 ft 8 in) | |
Cabin width, upper deck | 5.94 m (19 ft 6 in) | |
Wing area | 845 m² (9,100 sq ft) | |
Operating empty weight | 276,800 kg (610,200 lb) | 252,200 kg (556,000 lb) |
Maximum take-off weight | 560,000 kg (1,235,000 lb) |
590,000 kg (1,300,000 lb) |
Maximum payload | 90,800 kg (200,000 lb) |
152,400 kg (336,000 lb) |
Cruising speed | Mach 0.85 | |
Maximum cruising speed | Mach 0.89 | |
Maximum speed | Mach 0.96 | |
Take off run at MTOW | 2,750 m (9,020 ft) | 2,900 m (9,510 ft) |
Range at design load | 15,200 km (8,200 nmi) | 10,400 km (5,600 nmi) |
Service ceiling | 13,115 m (43,000 ft) | |
Maximum fuel capacity | 310,000 L (81,890 US gal) | 310,000 L (81,890 US gal), 356,000 L (94,000 US gal) option |
Engines (4 x) | GP7270 (A380-861) Trent 970/B (A380-841) Trent 972/B (A380-842) |
GP7277 (A380-863F) Trent 977/B (A380-843F) |